Door handles locks the outer casing or housing for motors pumps etc wheels of many cars. CO3 Analyze the design considerations for casting and welding process.
Design Consideration For Casting
Flow of the molten metal in the mould cavities the gating systems the rate of cooling and the gases evolved would influence the quality of a casting All casting operations share the characteristics of phase change and thermal shrinkage during the casting cycle But each process will have its own design considerations Design Considerations in Casting The general design.
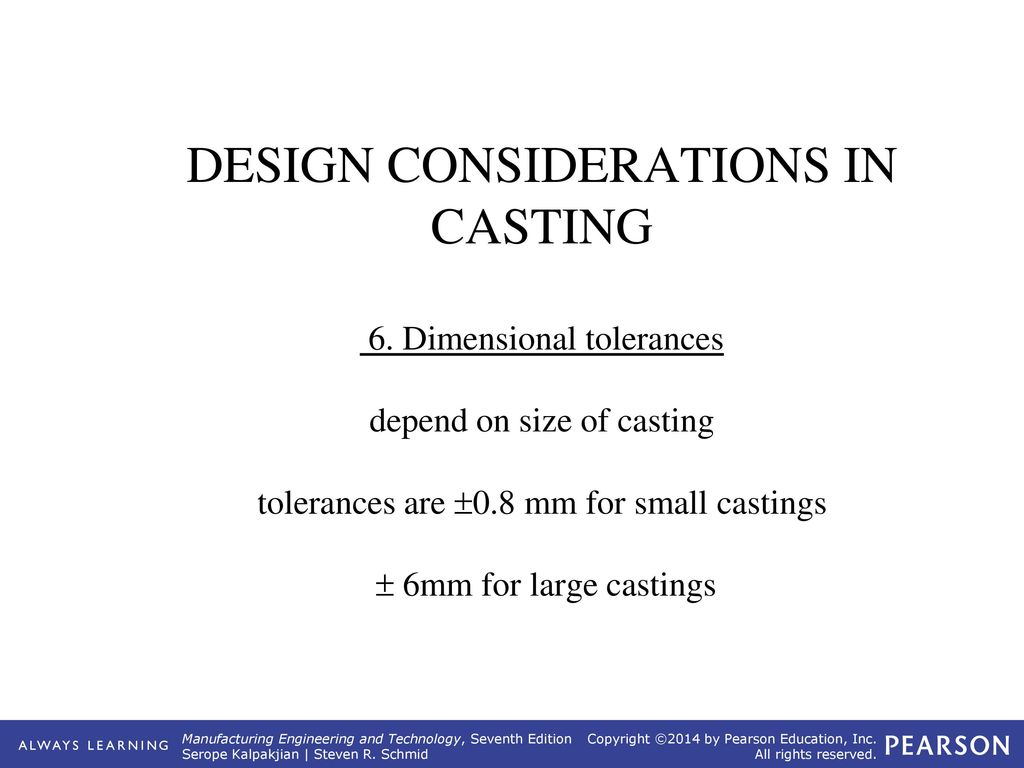
. Always try to introduce drafts in the process as early as possible. Different Methods to design Riser in casting is discussed. Riser Design Casting Definition.
General design considerations of casting are as follows. Design of component in. Hence design the parts such that stressed areas of the parts are under compression rather than under tension.
Some of these processes are die casting process investment casting process vacuum-sealed moulding process and shell moulding process. Winner of the Standing Ovation Award for Best PowerPoint Templates from Presentations Magazine. The parting line should be identified on the casting drawingDetermining the position of the parting line is a critical step in the casting design.
Tabs must be at least 2 times the sheets metal thickness or 0126 32mm whichever is greater and can be no longer than 5 times its width. Basic Requirements of Casting Processes Six basic steps of casting 1. It is very important for GATE mechanical exam.
Many new casting processes have been developed which can take into consideration the aspects of dimensional accuracy and surface finish. The cast iron is much stronger in compression than in tension. Design is a crucial step in the manufacturing of high-quality castings.
Avoid using sharp corners and angles as they act as stress raisers and may cause cracking and tearing during solidification. Design Consideration In Casting Ppt. Always Keep the Stressed Areas of the Part in Compression Cast iron has more compressive strength than its tensile strength.
Locate the parting line of the mold in the part. Sharp corners are avoided to reduce the stress consideration. Curls dimension outside radius must be at least twice the materials thickness.
General Design Considerations The development of a complete plant design requires consideration of many different factors such as. Locate and design the gates to allow uniform feeding of the mold cavity with molten metal. They are all artistically enhanced with visually stunning color shadow and lighting effects.
A Casting can produce very complex. Construction and operating costs The cost of construction can be minimized by adopting a layout that gives the shortest run of. O s Course outcomes CO1 Understand various general design rules for manufacture ability and criteria for material selection.
This element prevents the casting from getting trapped in the mold or tool during the ejection of the casting making it much easier to open the die and easily eject the casting from the die casting die. We covered the creation of patterns and the setup of the mold and gating system. 4 Advantages of casting.
Give fillet wherever the sharp corners are present. Avoid Concentration of Metal at the Junctions. Metal casting is a labour intensive process.
The drafts start from the parting line. Worlds Best PowerPoint Templates - CrystalGraphics offers more PowerPoint templates than anyone else in the world with over 4 million to choose from. Avoid abrupt changes in the cross-section.
Design parts to be compression than in tension. Riser is defined as a reservoir for supplying molten metal to the casting cavity to compensate additional molten metal the liquid shrinkages taking place due to solidification. CO4 Apply the conceptual design factors to be considered in forging extrusion and sheet metal.
Design modifications to avoid defects in castings. Design Consideration In Casting. Parting line should be selected carefully so as to allow as small portion of the pattern as far as possible in the cope area.
Design Consideration In Casting-General tips For Casting Design. Theyll give your presentations a professional memorable appearance - the kind of sophisticated look that. Use of External devices for strengthen the part under tension.
The balanced sections with equal areas in tension and compression are not suitable for cast iron components. When Sheet metal parts have sharp corners try designing a fillet half of the material thickness. Toy cars planes etc.
When designing casting the most important consideration is the effects of shrinkage during cooling. Our new CrystalGraphics Chart and Diagram Slides for PowerPoint is a collection of over 1000 impressively designed data-driven chart and editable diagram s guaranteed to impress any audience. The general principles for the design of casting.
In this video we will learn the following topicsa. Construction and operating costs. Parting line should be selected carefully so as to allow as small portion of.
Up to 24 cash back Design Considerations in Metal Casting Mold and Gating System Design Directional Solidification and Troubleshooting In the previous sections we discussed the fundamental aspects of manufacturing parts by metal casting. As a company specialising in investment castings Dean Group know how important it is to get the. Design the part so that the shape is cast easily.
We covered the creation of patterns and the setup of the mold and gating system. General design considerations of casting are as follows. The parting line should be decided by the casting component design engineer and should be shown in the casting drawing.
Product Design Considerations in Casting - Geometric Simplicity Corners Section Thicknesses Draft. Select a casting process and material suitable for the part size mechanical properties etc. Design of component in compression than in tension.
And in order to design successful castings its necessary to use all the tools at our disposal including sophisticated simulation software. All Abrupt changes in section of the pattern should be avoided as far as possible. Avoid Very Thin Sections.
Shot Blast the Parts wherever Possible. Basic design considerations of the part and the entire casting process. Design Considerations in Casting 1.
Therefore section changes in castings should be blended smoothly into each other. Melting process Provides molten material at the proper temperature 3. Design Consideration In Casting-General tips For Casting Design.
CO2 Apply various machining process and tolerance aspects in machining. Other important factors include metal flow and porosity. The term casting is commonly used for metals and the term molding is used for plastics Examples.
Many of them are also animated. Top Design Considerations When Manufacturing Castings. Provision of Fillet Radius.
Ideally the position of the parting line should be such that the height of the mold box should be minimum or in other words the draw distance of the mold box should be minimum. The following considerations should always be kept in mind while designing a pattern. Mold cavity is produced having the desired shape and size of the part Takes shrinkage into account Single-use or permanent mold 2.
Door handles locks the outer casing or housing for motors pumps etc wheels of many cars. Casting is also heavily used in the toy industry to make parts eg.
Chapter 12 Metal Casting Design Materials And Economics Ppt Download
Design Consideration For Casting
Chapter 12 Metal Casting Design Materials And Economics Ppt Download
Design Consideration For Casting
Casting Design Materials And Economics Ppt Video Online Download
Design Consideration For Casting
Design Consideration For Casting
Ppt Design Considerations Powerpoint Presentation Free Download Id 6931310
0 comments
Post a Comment